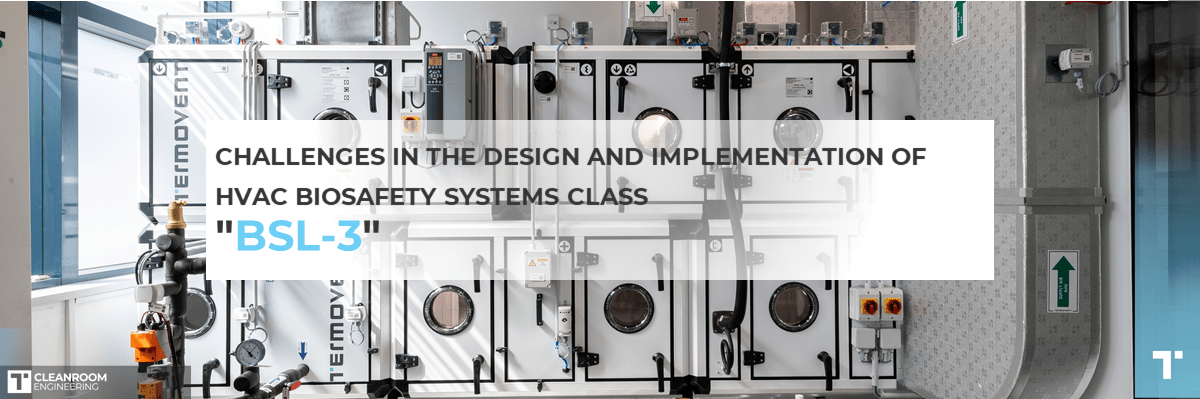
CHALLENGES IN THE DESIGN AND IMPLEMENTATION OF HVAC BIOSAFETY SYSTEMS CLASS “BSL-3”
Project: Building X
Many years of cooperation and partnership with one of the largest science and research parks in the Netherlands, this year has been completed with another completed project – the reconstruction of the building “Building X” (BSL-3).
Namely, before the start of the pandemic during 2017/2018 in the Netherlands, there was a need to build a new multifunctional laboratory that would meet the state’s needs in the fight against new, still unexplored viruses that could be a threat to the public health of the nation. The existing capacities of the current mobile laboratory for “quick response” have been dilapidated and with outdated technological equipment. The location of this science and research park was an ideal solution.
“Building X” within the complex, area of approx. 500m² at the base, on 2 floors, was chosen as a suitable location with appropriate architecture to accommodate the laboratory with accompanying technological equipment, HVAC systems and other mechanical and electrical installations required to meet the requirements of biological safety class 3 (“BSL-3“).
The preliminary design was entered in 2019 with the idea of using only the ground floor and the 2nd floor. On the ground floor of the building, a laboratory for “quick response”, “Kill Tank” room, electrical and server rooms, rooms for storage of process equipment, office, kitchen and toilets were planned, while on the second floor, on the so-called technical level, HVAC systems with duct distribution, filter units, compressor station, mechanical and electrical installations were planned.
With the beginning of the pandemic that year and the accelerated needs for research work in the field of vaccination, a decision was made by investors to form 4 new laboratories on the first floor of the building for the possibility of studying, manipulating and storing “live” viruses. Something like this was very convenient from the aspect of the existing investment in the original BSL class 3 laboratory. The preliminary design only needed to be scaled and supplemented to the full capacity of the building.
The scope of Termovent’s contracted work consisted of the following systems/units:
· Delivery and installation of Hygiene type air handling units with HEPA filtration and accompanying ductwork of galvanized ducts on the thrust and stainless steel ducts on the suction. Total capacity (7 systems / 26,000 m³/h / purity class “D” and “C” according to GMP)
· Delivery and installation of cold water sources (7/12 ºC), construction of heat substation with connection to the primary circuit of the heating plant (80/60oC), secondary circuit of installations with collectors/distributors, circulation pumps and fittings for connection to heat exchangers.
· Delivery and installation of electrical cabinets with automation equipment and peripheral sensors, two HMI panels with control software, SCADA monitoring system and AMS alarm notification system (via SMS messages or e-mails).
· Delivery and installation of cold sanitary and technical water tanks, generators and tanks of hot sanitary and technical water, distribution of softened water, as well as power supply system with “booster” pumps.
· Delivery and installation of space decontamination system with hydrogen peroxide vapor with generator, piping and fittings.
· Delivery and installation of inert gas fire extinguishing system in the “BSL-3” zone with gas cylinders, piping and fittings.
· Delivery and installation of duct fan-convectors for comfortable air conditioning of the office, kitchen and other non-classified space. Air conditioning split system server room. Cold room cooling system (2-8 ºC).
· Delivery and installation of local exhausts from laboratory hoods and cabinets.
· Validation of all mentioned systems according to GMP standard.
Each of the units has required special attention during the design and execution with regard to the main feature of each “BSL-3” laboratory, which is the maintenance of negative pressure (under pressure) inside the room in relation to the environment in all conditions of normal and emergency modes (accident).
The air part of the HVAC system had to be designed as single-pass, without recirculation. Each laboratory was designed with its own, local air handling unit which maintains the required parameters in the room – temperature, relative humidity, pressure and number of air changes. Thermally prepared fresh air was delivered to the local chambers from the central chamber. The central chamber for fresh air preparation consisted of three fan sections of designed capacity so that two of the three always meet the needs of the nominal flow of the installation, thus achieving redundancy. An identical set of chambers was located on the central exhaust from all rooms. To save energy, the heat of the exhaust air was recovered through highly efficient glycol exchangers, mounted on the main discharge and exhaust ducts. As the basis of any biological safety is the preservation of the integrity of the protected zone, areas and surfaces exposed to potential contamination had to be perfectly sealed, and airtight to the outside environment. The protection boundary consisted of channel HEPA H14 filters housed in stainless steel filter housings. Stainless steel exhaust ducts welded at each joint formed one unit with the contamination zone. Exhaust duct networks as well as HEPA housings had to be subject to a strict airtightness standard, similar to what is required in nuclear facilities.
When we talk about the redundancy of the system and “fail-safe” design, and above all the requirement that the pressure in the space must be preserved in every situation, we would like to mention the following technical solutions:
· redundancy of main air chamber capacity and effort,
· redundancy of main suction chamber capacity and effort,
· high-class non-return valves on the discharge line towards the BSL-3 room,
· constant flow regulators (CAV) of high sealing class on the pressure branch of BSL-3 rooms
· variable flow regulators (VAV) of the highest sealing class on the exhaust branch of BSL-3 rooms.
The water part of the installation followed completely high requirements in design and construction, where the company Instalater from Belgrade participated as a partner – subcontractor. For the production of cold water, three air-cooled chillers were planned with a designed capacity so that two of the three always meet the needs of the nominal flow of the installation, thus achieving redundancy. Cold water was distributed by means of a working and backup pump through pipelines to all consumers in the building. The primary distribution brought to the facility from the local heating plant was used as a source of hot water, while Termovent designed a substation for summer and winter operation as well as distribution to consumers. Sanitary and technical water systems were supplied from the city water connection. Independent tanks with their own “booster” pumps were designed to maintain the pressure of sufficient capacity to support the simultaneous operation of all showers required when leaving the BSL zone. Hot water heating in separate tanks was solved by means of a spiral pipe steam-water exchanger.
Electrical cabinets were designed with Schneider power equipment and Siemens Simatic S7 PLC as well as cards for receiving and sending digital and analog signals. Five PLC controllers are in charge of collecting and processing more than 750 IO signals of various actuators, peripherals and sensors. Fans with integrated frequency control of Ziehl-Abegg motor power, type GR, were used in all local chambers as well as in the main fresh air chamber, while the main exhaust air chamber were equipped for external frequency controller type Danfoss and motor/fan Ziehl-Abegg, type ER. SCADA and management software were developed in cooperation with our partners from Belgium, Actemium from Liege. The user interface was provided with accessibility via:
· Two Touch panels placed at both ends of the technical floor,
· SCADA computer from the local operator room,
· Remote access.
One of the specifics of the design, which Termovent encountered for the first time, was the clean space decontamination system. The working principle was developed in cooperation with partners – subcontractors on the project, the company Steris from the USA. The solution for decontamination of the space was through an open process of injecting steam ~ 30% hydrogen peroxide solution into the supply air stream.
Another specificity of the project, with which Termovent already has experience from one of the previous projects for the same client, was extinguishing the fire with inert gas in a clean space. The use of sprinkler systems and uncontrolled water jets for firefighting in BSL-3 zones was prohibited due to the possibility of environmental contamination. In this case, inert gas extinguishing systems developed by Tyco from the Netherlands, our partner and subcontractor on this project, was designed. A fire alarm initiates an extinguishing sequence that works in conjunction with the HVAC system. The sequence begins with the preparation of the space for the reception of inert gas whose task is to bind oxygen molecules in space and thus extinguish the fire. The HVAC system prepares the space creating a large under pressure in the extinguishing zone at ~ -400Pa. Gas-filled cylinders located on the technical floor connected to each other by extinguishing zones, distribute gas to each room. Gas fills the space at high speed through a nozzle mounted on the ceiling. After the gas is released into the room, the relative pressure in the room is maintained at ~ -80Pa. In no case after the gas fills the room, the pressure cascade in the rest of the building must be disturbed. The gas is retained in the space for the next ~ 10 minutes, after which it is flushed by aeration (supply of fresh air).
Unclassified general purpose spaces were air-conditioned by duct fan-converters connected to the control system. The supply of fresh air in the rooms where the users stay was designed from a dedicated air chamber with the rotary recovery of waste air energy. The server room was air-conditioned with a classic split system, while the cold room in which the temperature regime is maintained at 2-8oC was made with an external compressor-condensing unit and an internal evaporator.
The validation of the system was done according to the GMP standard with the partner laboratory LabProva from Belgrade accredited by ATS. Validation was performed with proven parameters of temperature, humidity, pressure cascade and number of particles in space.
A special challenge on this project was the period of the beginning and the logistical organization of the installation on the facility, which took place in parallel with the beginning of the COVID-19 epidemic in Serbia. In the most uncertain period and suspension of all trips throughout Europe, Termovent managed to export and deliver dozens of trucks of its own equipment and materials, send a team of fitters and engineers to the Netherlands and thus meet the requirements and needs of the client in emergency situations. With a systematic approach to the project, plan, organization and technical support of all colleagues, the project was successfully completed, and the client received an outstanding facility capable of meeting even the most stringent requirements in terms of biosafety standards, reliability and system management.
PROJECT IN NUMBERS (BSL-3 project)
· Beginning of the project: 08/06/2020
· Completion of the project: 30/12/2021
· The project includes: Air handling units, duct distribution, cold and hot water sources, water distribution, electrical cabinets and automatic control equipment, software, clean space decontamination system, inert gas fire extinguishing system
· Classes: D and C according to GMP classification
· Air handling units: Termovent Hygiene: pro
· Air flow: 26 000 m³/h
· Base area of clean rooms: 500 m²
· Area of technical rooms: 160 m²
· General purpose room area: 230 m²
Colleagues who shared with us the experience of working on this project
Slaviša Stanković
Project Manager
Nemanja Spasojevic
Project Manager
Nenad Vuković
Site Manager
© 1993-2020 by TERMOVENT Komerc d.o.o. All Rights Reserved. Powered by Combo