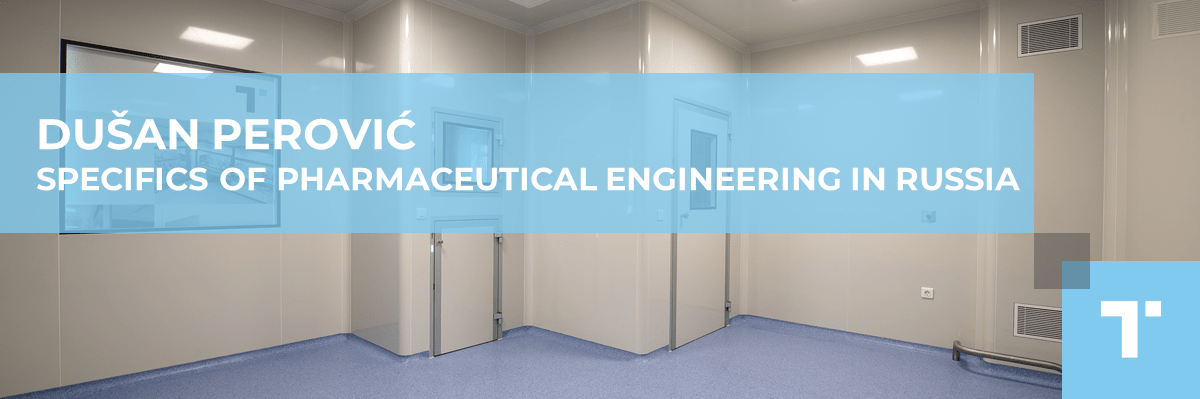
Dušan Perović – Specifics of pharmaceutical engineering in Russia
Termovent has been present on the Russian market for more than 5 years. During that time, we have had a large number of projects and collaborations with renowned partners. Together with our partners, we have become a relevant player in a very demanding market and we are very proud of the partnerships with the companies: Pharmasyntez, Katod, Evalar, Grand Medica, etc.
Below you can read the interview of our founder and president Dušan Perović for the Russian portal GMP News.
Please tell us something about Termovent products for the pharmaceutical industry. What modern solutions do you offer to drug manufacturers?
Termovent is a technologically modern production company with a large number of generation 4 CNC machines and that ranks it among the largest production companies in the region and beyond. A large number of constructed facilities in the EU, RF, SA, Emirates, India, etc., including quality human resources in all segments: design, production, execution, BMS / EMS, commissioning, has positioned our company at the very top of companies dealing with design, production, delivery, installation and commissioning of all systems for the purpose of providing parameters for the operation of each pharmaceutical capacity.
I will try to explain briefly what sets our company apart:
DESIGN, URS, ROOM DATA SHEET …
Our company applies its vast experience gained in a large number of projects in the EU with very demanding companies and each project is in accordance with the valid regulations, primarily GMP, FDA.
The biggest mistakes are made with accelerated design and incomplete projects, which are made only for passing the expertise and that brings with it a relatively lower design price but the first savings and the final required parameters are achieved only with quality and meaningful design because it finally gives constant quality, reliable system operation and high regularity.
We obligatorily process every design that we did not create, bring it within the required quality, coordinate with the client and only after that, we start production. Quality URS and ROOM DATA SHEET are certainly extremely important starting documents that are agreed with the client and they provide the required quality later in the development of the design.
Termovent starts every design in this manner and we have no other alternative.
EQUIPMENT QUALITY
Our company selects and installs only the components that are most used in pharmaceutical factories in the European Union for the formation of its products, such as air chambers, clean room panels, etc., and the choice of such components creates a precondition for the final product to be of the required quality.
AHUs (Air Handling Units):
I wouldn’t like to spend a lot of time talking about them now, except for a few important notes:
– All drive fans are with direct connection of motor and rotor, frequently guided according to the criteria of (most often) constant flow;
– The panels are of high quality with PVC protection of 110 microns, lambda sensor;
– The construction is made of Al profile, we avoided the possibility of oxide formation and particle generation;
– The inside is most often made of stainless steel;
– Each AHU has a PVC tub which prevents water spillage and thus we protect expensive technology, which is most often under chambers, from immersion and major damage. A water presence sensor is installed in the tub and we get information on the BMS;
– Our AHUs carry the EUROVENT logo.
CLEAN ROOMS:
The qualities that set our clean rooms apart from the others are:
– The supporting construction of wall and ceiling panels is made of Al profiles, special constructions that provide static load-bearing capacity, easy and high-quality interconnection;
– The filling of our panels is mineral wool, bulk density of 110-130 kg / m2. It all depends on the fire qualification, which also provides excellent thermal characteristics;
– Protective steel sheets are 0.80 mm galvanized steel sheet, protected by high-quality PVC foil, 110 microns thick, with a micro-embossed texture, which significantly reduces the impact of reflection from stainless steel surfaces of technological equipment and creates a pleasant environment for operators;
– The wall panels are supplied with electrical ducts inside the panels made of AL profile l = 80 mm which enables the easy supply of cables for the needs of switches, plugs, network;
– For all elements on the ceiling, there is a factory preparation of openings for their installation and nothing is done on the building itself, which completely eliminates the generation of particles.
BMS/EMS:
We do BMS management system and EMS monitoring system with the highest quality equipment: PLC configurations, sensors, licensed software, as well as excellent equipment, as follows:
– PLC configurations: SIEMENS
– Sensors: SIEMENS / REGELTECHNIK
– Actuators: SIEMENS
All this written above provides the required quality of the final design and any possible savings on the quality of the initial components is certainly reflected in the quality of the design.
How interesting and how difficult for your company has the clean room market proved to be in Russia and the CIS countries? Can it be compared to Serbian and European markets?
Personally, I think there is no company which is not interested in a huge market such as the market of Russia and the CIS but the basic problems we encounter are the following:
– A large number of investors choose architecture design offices with which they achieve a lower design price and thus we obtain undefined conditions for execution and the quality of the equipment that is installed;
– The different qualities of the equipment offered to the investor with such design specifications certainly create a bad image among investors about the bid amounts from different manufacturers because there is absolutely no talk of comparable quality;
– With due respect to all bidders for offers on projects in Russia, such as the equipment from Chinese manufacturers, I think the equipment from Russia is really of lower quality than equipment in the EU. I think that with very high-quality teams of your competent Ministry, which works on the acceptance of the facility and issuing decisions and certificates for production, these qualities will be harmonized very quickly;
– A sure reason why these companies do not exist in more demanding markets, such as the EU, is certainly the lower quality of equipment.
Our company has an absolutely equal quality of equipment and performance in the EU and all other markets for which we work, such as Russia, Saudi Arabia, UAE, India … and that creates certain problems for us due to the difference in the bid amounts.
What experience do you have in good engineering practice? How is your company different from the competition?
Our experience in good engineering practice is extremely extensive because we are a company which has performed and validated over 150 companies in the EU alone and the requirements of these companies are extremely high as well as the validation teams that perform external checks and controls with full application of all relevant regulations defined in the GMP.
The differences between our company and the other companies are mainly in the following:
– Extensive experience in preparing the necessary documentation for validation, which is done constantly from the beginning of the design, the execution phase;
– Teams for the preparation of validation documentation: EQL, IQ, OQ with the associated tests and protocols have certificates of professional competence for the development and implementation of the same;
– The traceability of each element in each document (TAG defined by it) is complete and it also significantly simplifies the validation process itself, making it easier for the investor to quickly detect through the TAG which element is in question.
In the EU there are no significant differences but in Russia, there are certainly differences in the content and quality of validation documentation; in the execution according to valid regulations, the readiness of our projects for acceptance procedures by competent institutions is at a much higher level than other bidders;
I have to mention the company STI from Moscow, which has carried out a lot of projects in the Russian Federation and is one of the few companies that is qualified to carry out projects according to valid regulations.
Please tell us about the specifics of modular clean room technologies for the pharmaceutical industry: design and construction, validation, commissioning of facilities…
The quality of modular clean rooms is mainly reflected in the following:
– Firstly, the selection of a quality manufacturer of clean rooms, which has extensive experience in the most demanding pharmaceutical requirements, high-class cleanliness, a large number of performed laboratories with high protection classes (BIOSAFETY LEVELS 2, 3, 4) and thus the preconditions for the particle qualification of the premises to be safe and constant are already created, i.e. there are no air leaks between the rooms and GMP cross-contamination does not exist, the required classes of biological protection in laboratories are achieved thus protecting operators and the environment. This cannot be achieved by all clean room manufacturers and there are big differences;
– Quality design with defined basics of pharmaceutical space, schedule of personnel, materials and finished products, defined GMP pressure cascades that protect the mutual contamination of adjacent rooms, defined amounts of air on insertion and extraction provide class and maintenance of room class as well as the system recovery speed. These are all conditions that significantly raise the quality of the design and the final parameters;
– All my comments start with good designs so the performance with the selection of quality equipment and a quality contractor is certainly a precondition for the necessary final quality of the design. Not everyone can perform the pharmaceutical systems and I will again mention the very experienced and professional company STI, which is really able to carry out projects of great complexity and high requirements;
Validation is a process which begins with the design, with a unique tagging of each element and its traceability through the complete documentation.
The preparation of documents for validation with validation tests has to be done by an experienced team which has to be involved in all phases of the design. This is the only way to ensure the preconditions for the parameters to be within the technical requirements defined by the framework,
– I always emphasize the great expertise of the teams of your competent institutions in terms of design control and I personally do not see any differences in the expertise of the teams from Russia and the EU. This is to be commended.
– Commissioning the system is a very responsible process;
– The presence of programmers and electrical professionals is mandatory in order to possibly correct any observed deviation and bring it into the required range;
– The parameter commissioning team with calibrated measuring equipment checks each parameter and brings it, together with the programmers, to the technologically required range;
– A team of mechanical engineers harmonizes and solves any problem in the installations.
I am completely sure of my opinion that not every clean room has the same applicability and that differences and problems are noticed only with higher requirements, high class, high pressures in rooms and responsible biological protection classes in laboratories. Our rooms are applied in all conditions – the pharmaceutical production of preparations and laboratories of high complexity as well.
We are currently engaged in a large national project in the Netherlands, working on a whole set of virus testing laboratories, the COVID Laboratory as well as the emergency intervention laboratory.
One of the key elements in creating clean rooms is engineering systems. What technological solutions do you offer to your customers?
This is a very important issue that provides the end-user with a shorter lead time, simpler and easier installation and reliable operation of the equipment.
Our solutions are mainly contained in the basic design of the project if we are doing it and if not, certainly the proposal and harmonization of changes that provide all of the above. Our work with the company STI, and we do have projects they designed and the same is in case we design and they perform, implies maximum communication between the teams of our and their company in order to harmonize the details of our equipment that provide maximum quality, easy and fast installation, safe start-up and achievement of parameters.
Our equipment has all the constructive performances that enable, in addition to our engineering logistics, all of the above.
In conclusion, we would like to know your opinion on the prospects of pharmaceutical engineering in Russia and the CIS countries. What do you think – what is the demand for the services you offer to drug manufacturers?
I personally do not see any reason why pharmaceutical engineering in Russia and the CIS will not and cannot be identically developed as in the EU countries, to me it is the most competent group.
In my opinion, in Russia there are very high-tech production facilities, which can do quality pharmaceutical engineering, with the provision of the previous:
– Better and more meaningful design;
– The selection of quality manufacturers and this is in conflict with the views of many investors. They generally want it to be as cheap as possible without taking into account the significantly higher costs of exploitation of poor quality;
Making changes to certain legislation which is contrary to the requirements of GMP regulations, cases of support and extraction of air where such an approach constantly violates the particle qualification of aerosols from the air.
The EU does not do that and countries are no less responsible when it comes to fire protection;
– The responsibility for the deadline must be significantly improved, especially in the cases of smaller companies engaged in the development of canal distribution, pipe distribution because the quality and deadline for them usually does not exist and is not binding. Experienced companies like STI take care of that and they have almost all of it in their composition.
I am convinced that good pharmaceutical engineering in Russia is absolutely possible because the company STI, I mentioned throughout the text, confirms that.
The service of our company, especially because it has its own production of AHUs, clean rooms, air control elements, BMS / EMS with commissioning and parameter regulation, is certainly a need of every pharmaceutical company.
Our company contracts turnkey projects and we take full responsibility for ensuring all technological conditions, deadlines and quality.
This offer is attractive to all pharmaceutical companies, i.e. having one contractor with a huge reference, huge experience and its own production is certainly a popular offer for all pharmaceutical companies.
© 1993-2020 by TERMOVENT Komerc d.o.o. All Rights Reserved. Powered by Combo